
When a Calgary manufacturing facility decided to expand their production to include a new aluminum-aging batch oven, they called on Kristian Electric Ltd. to install a new overhead lifting system to handle bundles of aluminum as they are taken to and from the batch oven.
As this was an expansion of their existing production facility, the team at Kristian were tasked to find a crane solution that would fit amongst the existing machinery.
Workstation cranes can be installed beneath and around obstacles; featuring a pre-engineered modular design which can be easily expanded and relocated to any work area. Because of these adaptable features, Kristian selected a Gorbel freestanding workstation crane to fulfill the customer’s specific needs.
Columns are the ‘legs’ of the workstation bridge crane; anchored to the floor for support. Traditionally these legs are uniformly spaced to evenly displace the load-bearing weight, but Kristian had to find an alternate solution to accommodate the facility’s existing equipment.
Wayne Raber, Kristian Calgary’s Project Coordinator, installed each set of columns asymmetrically.
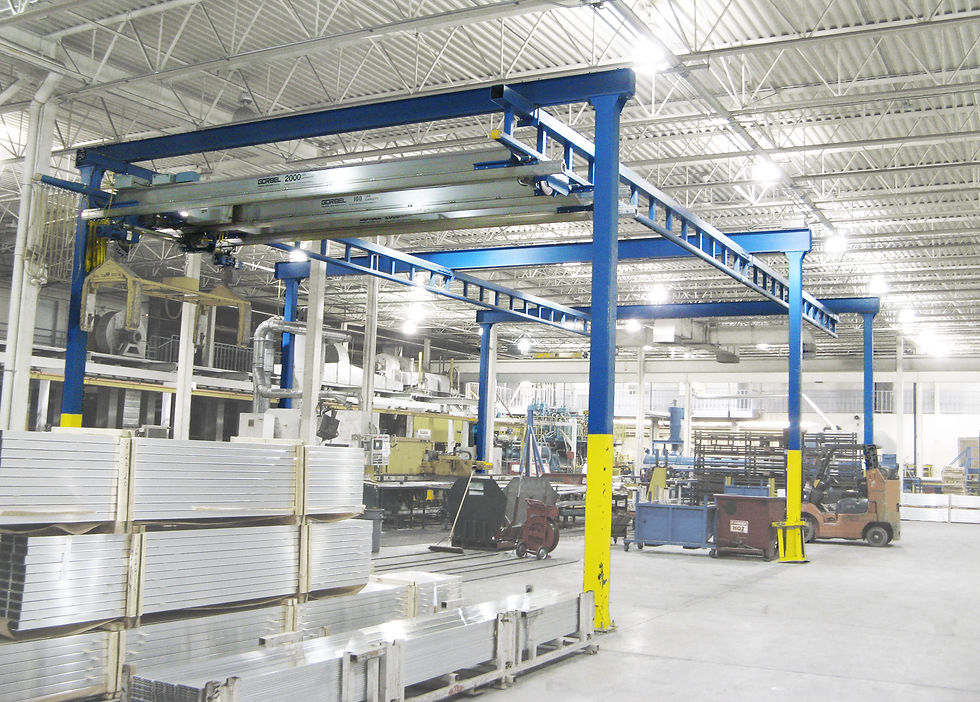
“All three column spacings were different to fit around the equipment,” he explains. “One end was 25’ center, the middle was 37’ center, and the other end was 35’ center.”
Raber’s staggered placement allowed the crane system to safely stand among the pre-existing fixtures without conceding any floor coverage.
Additional to the floor space constraints, the customer required an overhead lifting system that could be retrofitted to their customized lifting frame. The aluminum-bundle lifting frame was designed with two lifting points which could be manipulated evenly or incongruently. This variance was achieved with the inclusion of not one – but three – bridge beams.

The outer two beams, rated at 2000 lbs each, would sustain both hoists, the custom lifting frame, and the load. The center beam, rated at a mere 100 lbs, was specifically included to bear the tractor drives motorizing both the trolley and bridges. Not only did this modification line up perfectly with the customer’s lifting frame; it also allowed the crane to utilize the full distance of the runways.

“On most systems there is only one bridge,” says Raber. “The tractor drive is on one side or the other of each end truck. Incorporating a third centre bridge for the tractor drive allowed us to provide as much bridge travel as possible.”
Once the structural installation was complete, Kristian outfitted the new crane system with two Demag DC-Pro electric chain hoists. As a long-time loyal Demag user, the customer trusted the Demag brand as a reliable choice that would be easily maintained thanks to their convenient local distribution and service partner, Kristian Electric.
“The hoists, trolley drive, and bridge drive were set up with a radio remote control system,” says Raber. “The operator could select Hoist A, Hoist B, or select BOTH, so [the custom lifting frame] could be leveled if they were not synchronized.”
In the end, a few unique obstacles were met with even more unique solutions to tailor-fit the perfect overhead crane system for the customer’s needs.
Comments