In the summer of 2017, Hypertherm took a huge step forward in the plasma cutting industry with the release of their first, next generation mechanized cutting system, the XPR300.

A decade in the works, the XPR300 is the most digitally advanced system ever designed and built by Hypertherm. It's new design includes so much technological advancement that it currently has 22 new patents pending on it.
Even the company's CEO and President, Evan Smith has said that the XPR300 is the "Largest generational leap forward for plasma cutting technology in Hypertherm's history, or the industry's history".

X-Definition
The new XPR300 comes complete with X-Definition technology. Featuring a unique two-piece vented nozzle, which increases arc stability and energy density by aligning and focusing the plasma arc. Previously, this technology was designed for mild steel applications, however, it can now be applied to the full range of non-ferrous metals. Now creating a clean, sharp and consistent edge on stainless steel and aluminum as well.
Patent pending Vented Water Injection process reduces angularity and increases surface finish, especially on aluminum.
Patent pending Cool Nozzle technology provides liquid cooling direction to the nozzle bore, increasing cut quality and consumable life by over 40%.
New vent-to-shield technology mixes hydrogen reclaimed from the vented plasma gas with the shield gas to reduce angularity and increase edge consistency
Patent pending plasma dampening increases arc density and cut speeds
PowerPierce technology incorporates a liquid cooled shield to repel molten metal during piercing allowing for much a much deeper cut.
Advanced arc stability from a modified shield gas impingement
Enhanced tapered torch design that features a 76° included angle and bevel rotation of up to 52°.
True Hole technology incorporates new protocols to automatically produce bolt hole quality on mild steel with a diameter to thickness ratios of 1:1 up to 2:1.

3 Distinct Consoles
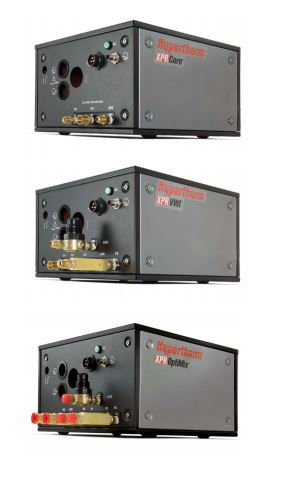
Core™ Unmatched mild steel cutting performance and superior angularity and edge finish on stainless steel up to 12 mm. This is delivered through a new N2 HDi™ process that prevents the mixing of air into the plasma gas, creating an improved, brighter edge finish.
Vented Water Injection™ (VWI) All Core console capabilities plus argon marking and a more than 10% increase in piercing thickness with argon-assist. Significantly enhanced stainless steel and aluminum capabilities are delivered with the addition of F5 HDi processes and patent pending Vented Water Injection (VWI).
OptiMix™
All the capabilities of the Core and VWI consoles plus discrete 3-gas mixing – Ar, H2, and N2 – for the world’s most flexible, premium stainless steel and aluminum cutting capability.
Twice the Performance, Half the Operating Cost
The new XPR300 has been designed to reduce operating costs by over 50%.
With 300 amps and 63KW of power, this beast of a machine delivers much higher cut speeds, up to 15% faster on thicker materials.
Higher quality cuts that reduce or even eliminate secondary operations.
By eliminating the impact of ramp down errors, consumable life increases of over 40%, compared to previous systems.
20% thicker piercing on stainless steel and 30% thicker piercing on mild steel
Quicker set up time to further cut operating costs.
For more information, download the comprehensive XPR300 brochure.
Source: www.hypertherm.com