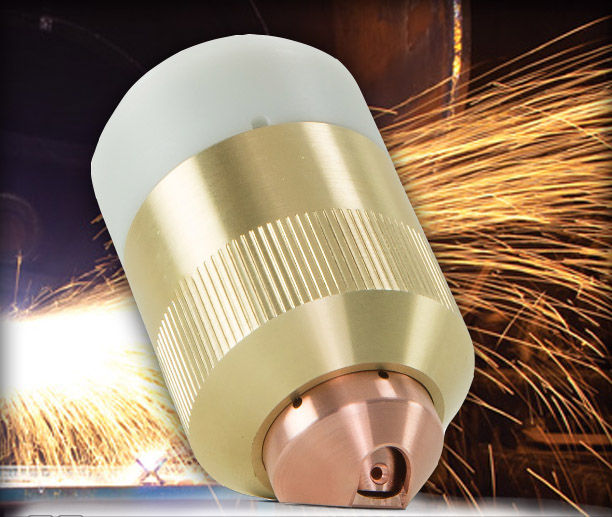
Traditionally, lug and attachment removal has relied on carbon arc gouging, oxyfuel and traditional plasma cutting equipment. However, these applications can be inefficient, time consuming and may pierce or damage the actual work piece.
With Hypertherms FlushCut consumables, you can eliminate these issues.

Designed with an angled nozzle bore and guiding flat to create the ideal positioning for a flush removal. A 45 degree angle creates the closest cut possible, leaving less than 5 mm (3/16”) of material behind. Such a small amount of residual metal significantly reduces time spent grinding and decreases total process time up to 50%.

In comparison to oxyfuel applications, FlushCut plasma cutting requires much less pre-processing time and reduces heat affected zones up to 10x less. With carbon arc gouging, multiple passes are needed to accomplish the same as a FlushCut plasma process can do in a single pass, not to mention the increased smoke and noise. While traditional plasma cutters only allow the user to cut at a steep angle, creating more need for secondary repairs, such as grinding.
Typical flush cutting applications include:
Removing lugs, pad eyes and temporary weld supports
Material washing
End cap removal
Rat hole cuts in I and H beams
Bolt and rivet washing
Casting sprue removal
Post tension cable tail cuts
Wearable part removal/replacement
FlushCut consumables can be used in both mechanized and handheld applications with the Powermax 105 and Powermax 125 plasma cutting systems.
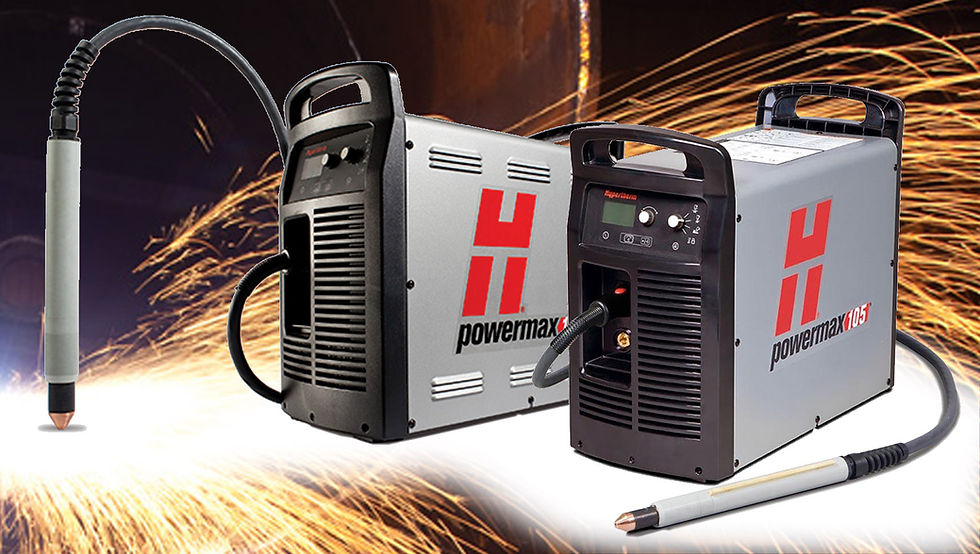